「NDT新思想」和你一起学习NDT!
在上篇文章中介绍集箱(管道)超声检测案例,不仅列举了“坡口未熔合”缺陷评定的步骤,更着重探讨如何建立分析缺陷的思维方式。
现在我们继续分析另一个典型案例,先简单介绍其检测背景。某火电厂压力容器定期检验,抽查2台低压加热器(简称低加,属于换热类容器,抽查部位的规格为Φ1500×36mm,材质为16MnR)的筒体环焊缝,焊缝为双面焊接,焊缝外半层为自动焊接,内半层为手工焊接,要对该环焊缝进行超声、磁粉检测等抽查手段。2台容器同一厂家生产。
磁粉检测发现焊缝外表面熔合线处,存在类似虚线式的磁痕,该缺陷存在一定深度,即为面积型缺陷,并且整圈焊缝断续存在。打磨一定深度后,细看缺陷形貌,很直,不具有裂纹的弯曲和尖端特征。下图为焊缝打磨一定深度,磁粉检测后的留下的磁痕(图片不清晰,请点击图片看大图)。
用K2的探头扫查该焊缝,同样发现整圈焊缝内部存在断续的超标缺陷,其中有两处长度分别为350mm和290mm的缺陷,此缺陷波幅很高,且超过定量线17~20dB,如下图。找到缺陷最高波后,移动闸门框住该波,深度读数为21.6mm(筒体壁厚36mm),水平位置距离焊缝中心2mm左右。由此可知,缺陷位于焊缝下半部分,处于手工焊接部位,缺陷深度和水平位置与其它断续超标缺陷基本一致。再换成K1的探头,发现也存在该反射波,但波幅仅位于I区或II区,与K1扫查缺陷的位置基本一致。由于结构受限,仅能进行单面单侧扫查。最后用直探头扫查,但未发现缺陷。
发现缺陷后,可借鉴《超声检测“坡口未熔合”实战分析(上篇)》判定缺陷的思路。
首先,了解焊缝的结构型式,排除特殊结构引起的结构波,可以查看图纸或者现场观察。该压力容器人孔门已经打开,我便钻进容器内部,查看内壁焊缝结构,发现该焊缝为双面焊双面成型,内层为手工焊接完成,除此之外,未发现特殊焊接结构。因此,可以排除特殊结构引起的结构波。
其次,了解焊接情况,磁粉检测发现熔合线处存在断续磁痕,非裂纹,那很有可能是坡口未熔合缺陷,并且超声检测通用发现许多超标缺陷。因此,可以判断该整条焊缝的焊接质量很差。
根据上述两个步骤可初步的判定为缺陷,但是仅从这两个方面判断不太严谨。应换不同K值探扫查,比如用K1的探头,或直探头扫查等,再或是其他检测手段,TOFD、相控阵、射线探伤等。
通过上述几个步骤,基本可以下定结论——该异常波肯定是缺陷波,缺陷性质为坡口未熔合。确定缺陷后,要对缺陷进行消除。
有人就会问,超声检测是一件很容易的事情,干嘛搞的这么复杂?发现缺陷直接挖不就可以么?
可能有人会认为,超声检测其实是一件很简单的事情,屏幕中出现异常波,管他是不是缺陷,直接开挖,挖出来了说明你的技术牛逼,没挖出来就怪工人打磨的速度太快,把缺陷一并给磨掉了,这既省时,又没有任何风险,何乐而不为呢?
我不完全否认这种做法是错误的,发现超标缺陷肯定是要消除的,这点没错。但是不经过仔细分析,而错挖焊缝,不仅影响自己的声誉,更多的会造成经济的损失。可能这种经济损失对自己没有直接的影响,但是换个思维方式,这种行为会不会影响自己的前途?这可是实实在的切身利益。
而我们搞在役设备检测,发现问题会再三斟酌,至少9成把握才能去挖缺陷。一般检测中发现缺陷,并打磨验证确实存在,业主会感谢你,但更多的会认为这是你分内的事,其实想想也是这样的。
如果你发现“缺陷”,却挖不出来会怎样?
发现“缺陷”没挖出来,有两种情况,一种是误判,另一种是真有缺陷,挖的太卖力,将缺陷一并挖掉了。不管是什么情况,业主只会认为你没有这个金刚钻,却揽了瓷器活。失去业主信任,可能下次就不会选择你们单位,对公司、对自己的损失非常大。这还不如不挖呢,设备带缺陷运行了五年十年的,没出现任何问题,不挖又有多大的影响呢?当然这是要承担巨大的风险,不值得提倡。
处理一个缺陷,是要付出很多代价,特别是电厂高温高压蒸汽部件,这类部件通常是采用高强度的合金钢,这种材料一般不会轻易处理。
一是这种材料可焊性差,需要热处理,控制不好容易,会导致焊缝硬度不合格,而这种材质热处理最多不能超过两次,如果再热处理一次不合格,那必须得换一段,耗费的巨大的财力。二是处理这类焊缝困难,处理不好会使原本好的焊缝变坏,处理时间长,影响工作进度…
所以我们检测中发现“缺陷”,通常会采用多种方式来验证,在没有十足把握之前,不会通知业主进行处理,而是向我们上级领导反映,派专家到现场实地勘察,有把握才会挖焊缝。这种做法看似繁缛,却是节约成本的一种高效做法。
扯了这么多题外话,回到案例中。当时打磨缺陷的工人是该厂的在编员工,他们也懂探伤。焊缝打磨一定深度之后,仅仅发现了两三点夹渣、气孔之类的缺陷。缺陷消除的过程,我不在现场,业主打电话给我,说没有发现所谓的“大缺陷”。虽然嘴上没说我们水平的不行,但是心里肯定犯嘀咕…但愿是我以小人之心度君子之腹吧。
此时,我再次提着超声波仪器和渗透剂赶赴现场,超声波检测发现仍然存在缺陷,但是缺陷长度和深度发生改变,没有原来那么长,并且深度更深了。渗透检测后,缺陷非常明显,见下图,缺陷正好处于坡口位置,且两侧坡口均存在缺陷。超声检测与渗透检测的结果基本一致。
最后引用黄建明先生在远东无损检测论坛提出的五个处理缺陷的方法和步骤,当然我也篡改了一点,这些步骤和方法是我们通常采用的,一并分享给大家。
第一步:超声检测(或射线检测)发现缺陷,现场标记缺陷位置、长度、深度、当量,并记录;
第二步:用射线(超声)或者其他手段(TOFD、相控阵等)确认缺陷,并对照超声检测结果;
第三步:气刨到接近的位置时(特殊情况只能用砂轮机),改用砂轮机打磨方法和配合磁粉或渗透检测追踪缺陷;
第四步:找出缺陷后,用相机拍照留档;
第五步:最后打磨消除缺陷后,再用磁粉核对是否完全消除缺陷。
我再加一步:缺陷处理并补焊后,再进行一次超声检测。
- 博主:曹智
- 个人资质: 特种设备UT-III、RT-III、MT-III、PT-III、PA-II、TOFD-II
- 原创说明:如需转载本站原创文章请联系博主!未经允许转载,将追究其责任!
关注「NDT新思想」公众号,更多干货等你来!
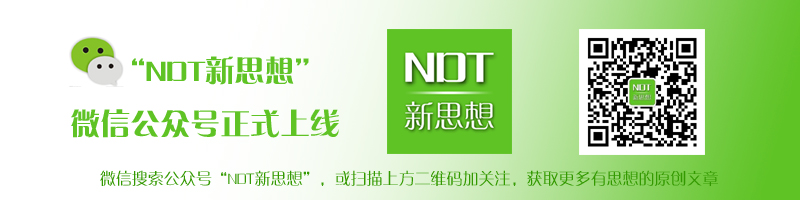
评论前必须登录!